This is a republish of a post from January 25th, 2007 for Houseblogs.net Fireplace tagging thingy:
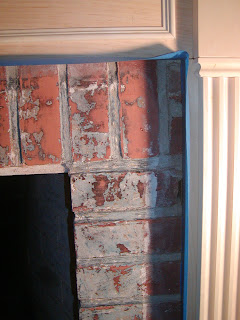
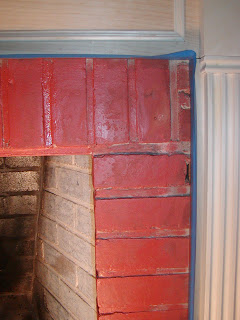
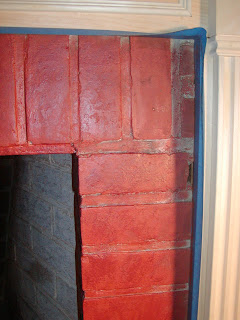
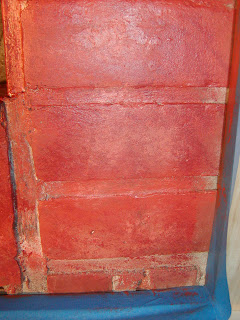
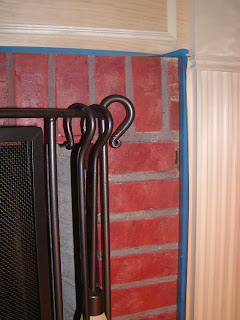
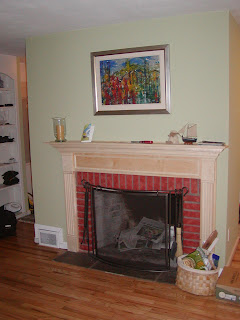
Slowly getting back into some projects after a lull over Xmas. Have mainly been concentrating on the kitchen project but last night I took on the brick surround on the fireplace (yet again). Last effort was four coats of paint stripper and no brick in sight (first two coats were an environmentally-friendly stripper that you left on for 24hrs til it changed color, 2nd two coats were a chemical stripper but still no luck.
I headed to Lowes and got some heavy duty (50) sand paper for the Mouse and also a bunch of brick red paint swatches. I sanded the brick a bit and results were mixed - some of the paint came off easily but some was on there for good so I decided I have to do the faux paint. Back to Lowes but this time I had matched the swatches to the actual brick tones and bought 3 sample pots of paint ($3.98 each and a "pouncer" brush to stipple - couldn't bring myself to drop $15 on a sponge). The mid color that I painted on first was American Century Tropical Nut, then a stippling of the just slightly darker Cliveden Henna Red and then a stippling over that of a slightly lighter color - Florentine Clay - that I softened and dispersed a lot more with the brush to get that kind of effervescence white sheen that you get on bricks.
I think the results were pretty good - the flash doesn't help the photo. I painted on the medium shade first and then stippled the darker tone on top and then stippled the lighter tone over that being sure to really work it so that it looked like a soft smudge and not edgey. The samples only came in satin but I didn't want to buy a quart of flat so I might have to hit it all with a matt clear top coat. Just need to go back tonight and get a cement color for the mortar and then I can start priming/painting the mantel/wood surround.
Went back to Lowes tonight with another matching color swatch but wanted to check if there was any ready-made mortar in a tub that I could use as the painting was going to be a pain. Luckily Lowes had Quikrete Textured Mortar Repair ($1.99) - think grey bath caulk with sand and grit in it. So I just smoothed that on with my fingers in to the mortar groove and wiped off the edges of the brick and I think it looks fab. It really needs a wash coat to cut the new and clean look, to give it a bit of grime so I will have to look into that but apart from that it was a much easier, quicker project than I had anticipated.
I have since added a faint glaze as I thought everything looked too new and clean cut. I went back to Lowes and picked up a small bottle of their premixed Antique Glaze, it's in the Faux Painting display area. I was originally going to darken some individual bricks to give it the reused chimney brick look but I just faintly added some "dirt" all over - bricks and mortar with an old towel and as with the paint colors worked it really well so that there were no hard edges or obvious splodges. Fireplace mantel has since been painted gloss white.